Challenges and Trends in Sustainable Aviation Fuels
Michael Blaisse, PhD, Fellow
March 2024
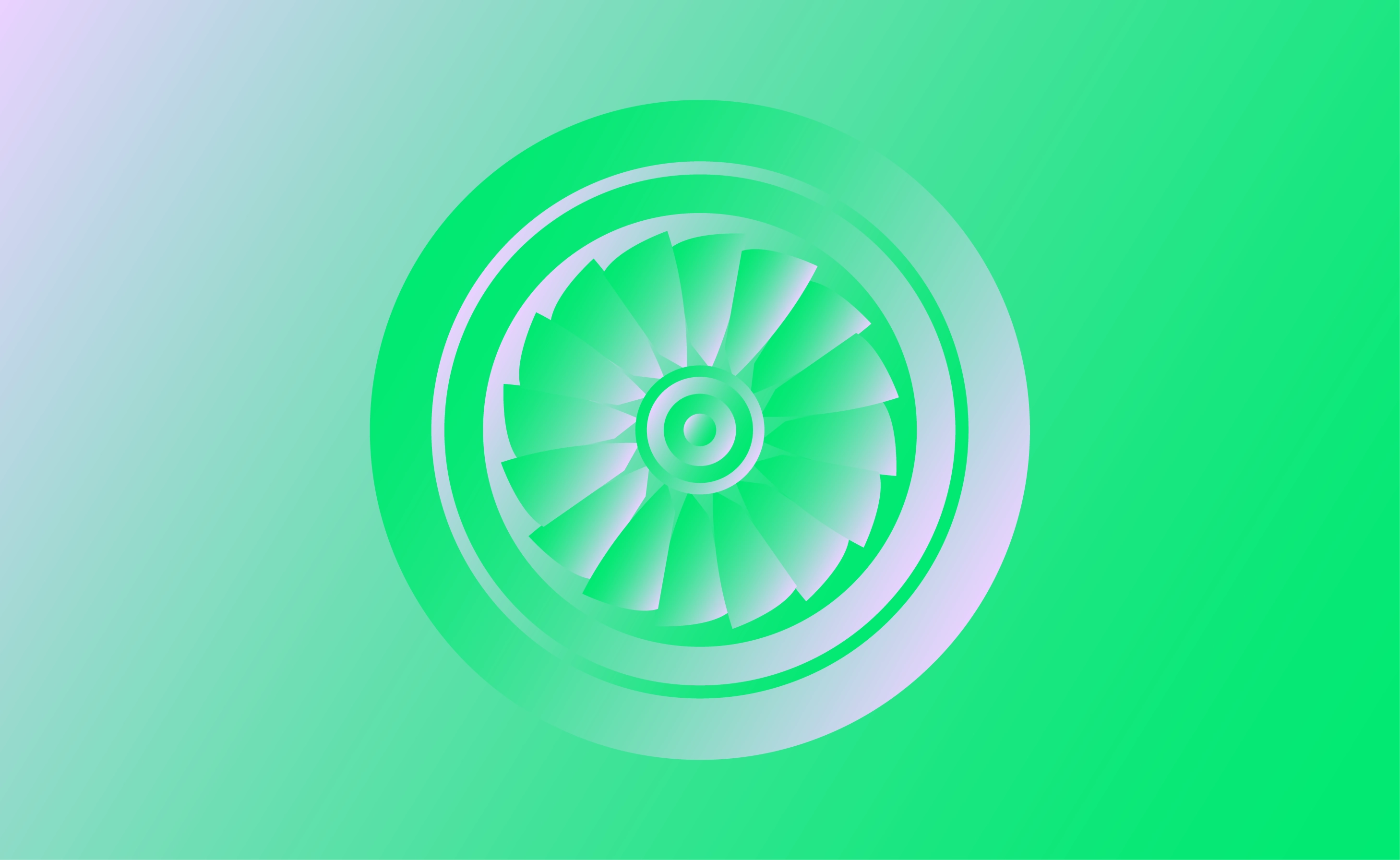
Introduction
As governments and consumers signal greater demand for sustainability in every part of the economy, aviation is no exception. Over 2% of global carbon dioxide emissions come from aviation, and major airlines and industry trade associations have set targets of net-zero carbon emissions for air travel by 2050. This requires switching away from fossil fuels toward sustainable aviation fuels (or “SAF”), such as biofuels or synthetic kerosene. Government incentives are also making the space attractive for investment. The 2022 Inflation Reduction Act (IRA), for example, offers tax credits of up to $1.75 per gallon of SAF (compared to jet fuel costs ranging from $1 to $4), depending on the extent of reduction in CO2 emissions.
Yet global SAF production was only 80 million gallons in 2022, less than 0.1% of the ~100 billion gallons of aviation fuel consumed annually. More than 130 SAF projects have now been announced that could expand annual production to as much as 18 billion gallons in 2028, but sustained growth and innovation are clearly needed to achieve net zero emissions targets. Technology to produce sustainable fuels has existed for decades. The question is whether it can be cost-effective, energy-efficient, and scaled to meet the rising global demand. This paper examines the technical and economic hurdles facing large scale adoption of SAF and the landscape of companies innovating to meet the challenge.
Background
Why SAF and Why Now
Why not transition away entirely from hydrocarbon fuel like today’s kerosene jet fuel and towards hydrogen or battery-powered aircraft? Two big reasons are the space and weight constraints of aircraft and the long development and investment timeline to onboard novel propulsion systems.
Commercial airliners require a power source with high energy density, especially for long-haul flights which contribute the bulk of the industry’s CO2 emissions. Hydrocarbon fuels are inherently advantaged in this regard. Compared to kerosene jet fuel, today’s batteries supplying equivalent energy would weigh 40 times as much. Liquid hydrogen would take up 4 times the amount of space and would have to be stored at a temperature of -250°C.
Hydrocarbon fuels can therefore be thought of as a kind of “liquid battery” that is especially stable, transportable, and dense.
But to put it in perspective, one gallon of kerosene would have the energy capacity of nearly 10,000 AA batteries (although electric motors are more efficient than turbine engines at using that energy).
Hydrogen propulsion also faces a chicken-and-egg problem. Airlines need to invest in new aircraft which still require decades of development, but they won’t do it until the infrastructure is ready for all of the airports where they might be used. And hydrogen may not be the clean-combusting fuel some imagine. Since it burns so hot, it can form more environment-damaging NOX emissions than hydrocarbon fuels do. Companies like ZeroAvia are paving the way for hydrogen-powered aviation with solutions like H2-electric engines, but there is value in enabling decarbonization with existing aircraft and infrastructure.
That’s not to say all the advancements and investments in clean energy and green hydrogen don’t have a role to play in clean air travel now. On the contrary, hydrogen is a key ingredient in most of the approaches to produce SAF, and recent innovations and incentives to reduce the cost of electrolysis are key enablers for why SAF has been receiving more attention.
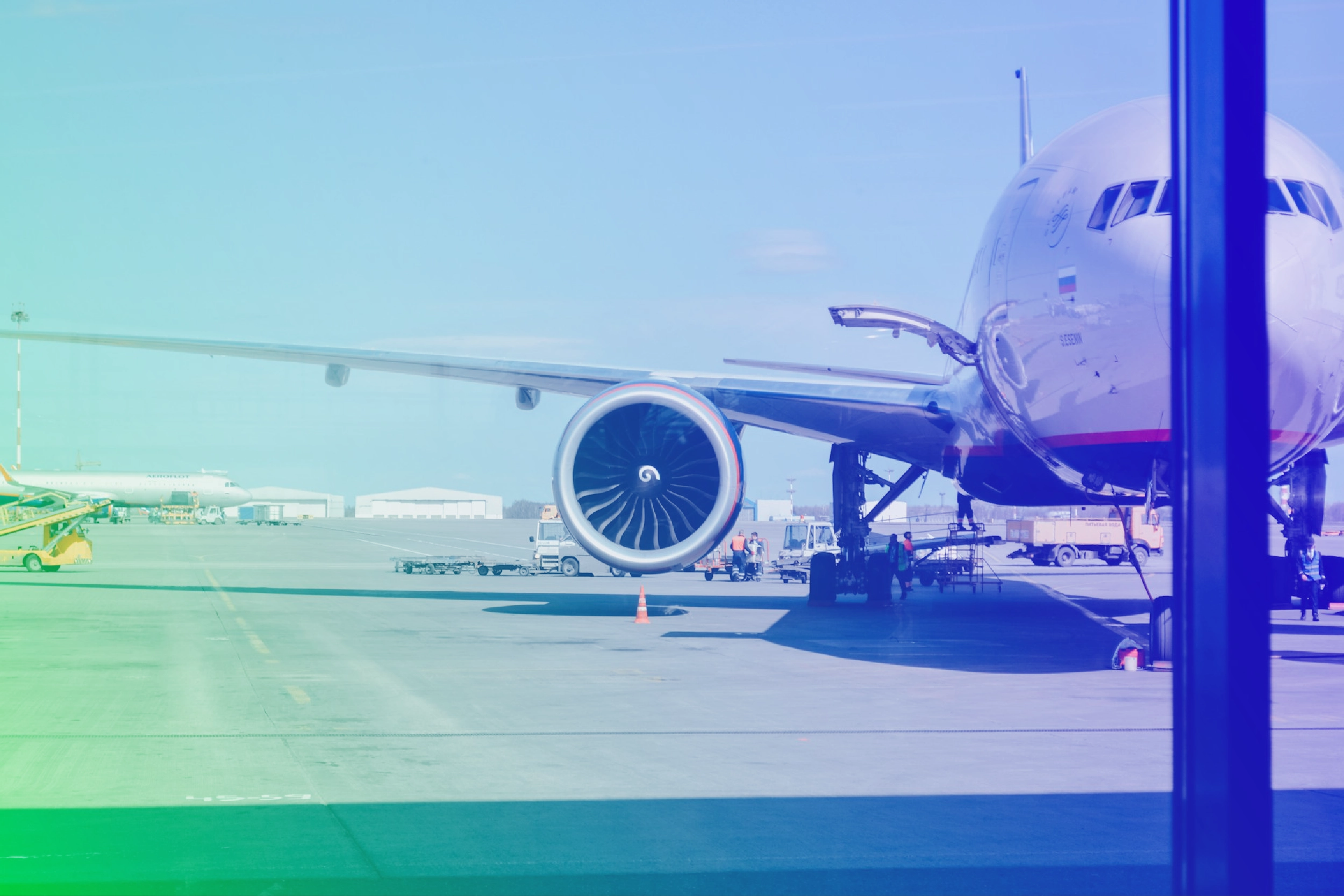
Carbon-Based Fuel as Part of a Circular Energy Economy
To see how SAF like biofuels or synthetic kerosene can be a part of a circular energy economy, it helps to think a bit about the chemistry of fuels and combustion. Transportation fuels are hydrocarbons, molecules containing primarily hydrogen and carbon atoms bonded to each other in chains of various sizes and shapes. When hydrocarbon fuel burns in an engine, it reacts with oxygen in the air. The hydrogen and carbon atoms break apart from each other and form new bonds with oxygen, producing water (H2O), carbon dioxide (CO2), and lots of heat (energy). The expansion of hot gases can be harnessed to, e.g., spin a turbine, push a piston connected to a drivetrain, or propel an aircraft from the thrust of the gases.
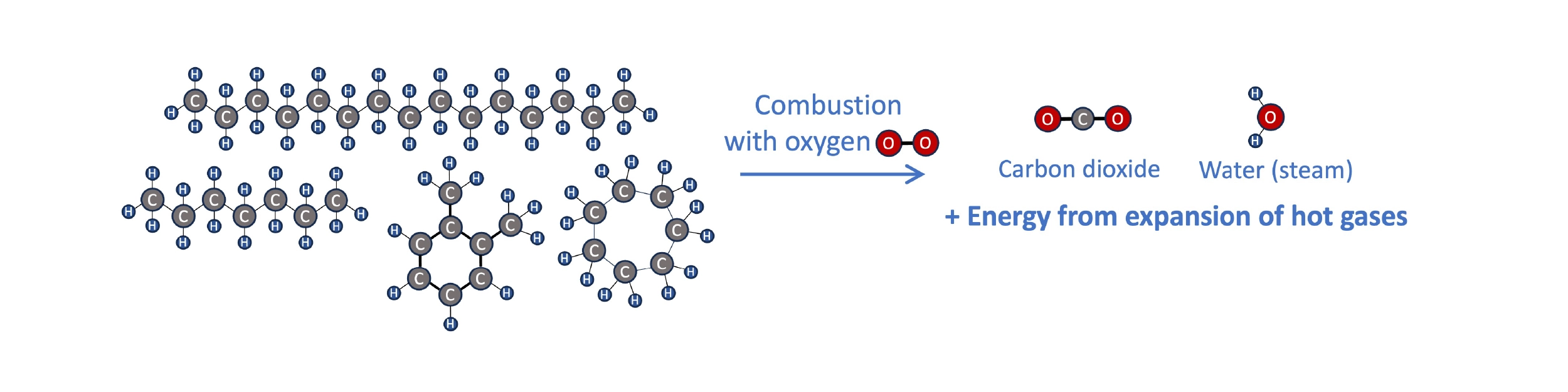
Combustion of hydrocarbon fuels in an engine produces CO2, water, and lots of heat. The energy from the expulsion of hot gaseous products can be harnessed for propulsion.
The path to sustainable fuel is exactly the reverse of combustion: energy is harnessed to convert the ingredients of water and CO2 back into fuel while putting oxygen back into the air. Whether this process happens inside a photosynthesizing plant or using electricity, the process is remarkably similar. Green plants and algae use the energy of the sun to split water, using hydrogen to fix CO2 into carbon-containing biomass like wood, starches, or oils, which can be converted into biofuels. Electricity can be used instead of sunlight to split water and captured CO2, first forming intermediates like hydrogen gas (H2) and carbon monoxide (CO) or methanol and then ultimately synthesizing a kerosene equivalent fuel. This latter process is often called power-to-liquid (PtL). In either case, H2O supplies the hydrogen content, CO2 supplies the carbon content, oxygen is removed, and energy is required.
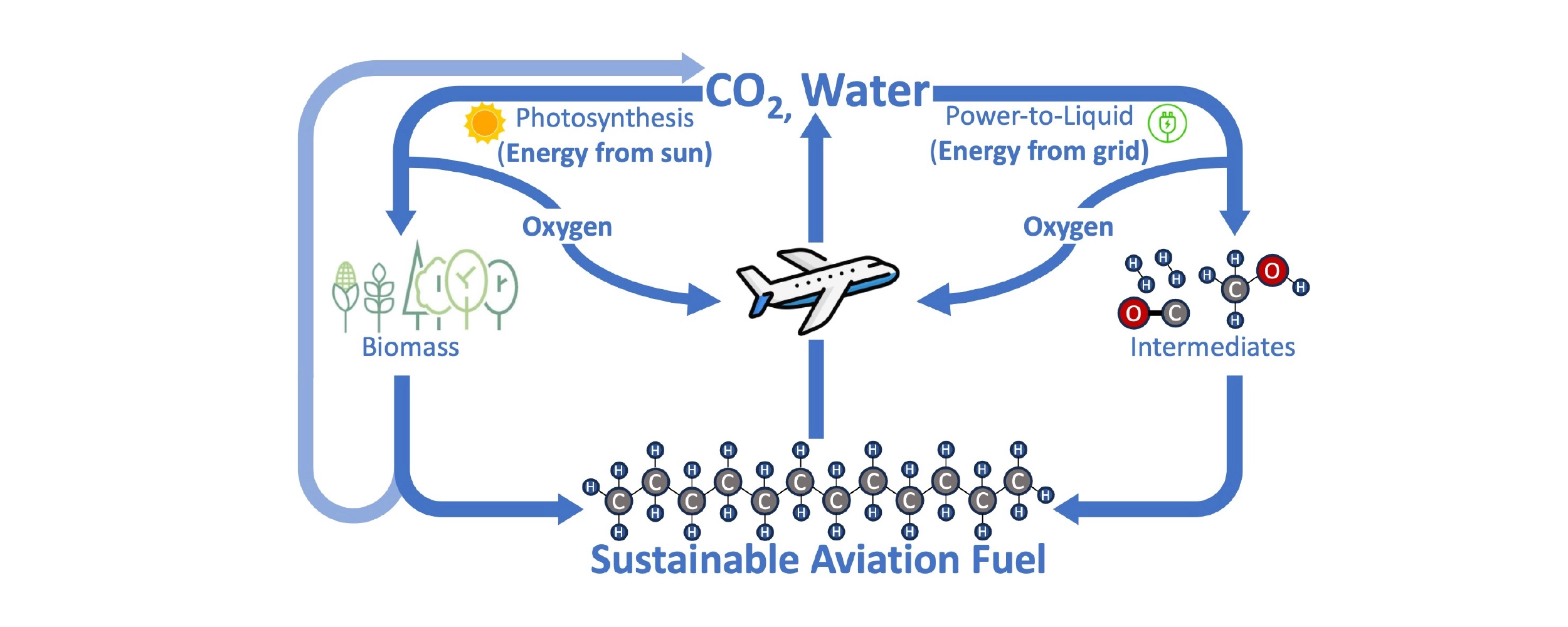
A circular fuel economy with SAF: Combustion with oxygen in a jet engine produces energy and emits CO2 and water. Energy from the sun or the grid can convert CO2 and water back to SAF and oxygen, either via biomass (e.g. wood, sugars, algae, vegetable oils) or a power-to-liquid (PtL) process. Processing to convert biomass into SAF also emits CO2, but the process can still be circular since the biomass originated from atmospheric CO2.
The overall process could be circular and sustainable if all carbon-containing compounds in the process originated from atmospheric CO2. This would mean all chemical reactors and other equipment in the production process would run on zero-emissions electricity and/or burn only fuels that are likewise sustainable. In practice, there are still lifecycle emissions inherent in all currently available renewable energy sources. Every step in a SAF production process must therefore be highly efficient, as any inefficiencies impact the yield and require overbuilding the feedstock or clean energy supply. Other barriers to sustainability (and cost) include whether the fuel composition of SAF can truly allow drop-in replacement and how to address other warming effects from aviation contrails related to fuel composition.
Composition of Fossil Fuel and of SAF
Different types of fuel (e.g. gasoline, jet fuel, diesel) have different compositions of hydrocarbons tailored toward certain physical and combustion properties. Since SAF is a product intended to replace fossil fuel, it helps to introduce some of the basic chemistry of fossil fuels, to give context for what SAF manufacturers are trying to produce and how.
Crude oil from the ground contains hydrocarbon chains of various shapes and sizes that can be separated by boiling in a distillation column and collecting fractions at different temperatures in the column. Lighter, or more volatile, fractions tend to comprise hydrocarbon molecules with shorter chains. The fraction called kerosene consists mainly of hydrocarbons with ~8-16 carbons and is the main component of jet fuel. It is intermediate between naphtha (~4-12 carbons), which is primarily used in gasoline, and diesel (~12-20 carbons).
Hydrocarbons can also be classified by molecule shape, which has an impact on a fuel’s properties. Jet fuel contains a mixture of paraffins (straight-chained hydrocarbons) and isoparaffins (branched hydrocarbons), as well as aromatics (e.g. benzene, toluene, xylene) and some naphthenes (a.k.a. cycloparaffins). These compounds are all found in crude oil, but fuel composition can also be modified through operations at an oil refinery. Hydrocracking enables the breakdown of heavier paraffins using a small amount of hydrogen, and an isomerization unit can convert paraffins into branched isoparaffins. Aromatics can also be synthesized through catalytic reforming of hydrocarbons in the naphtha range.
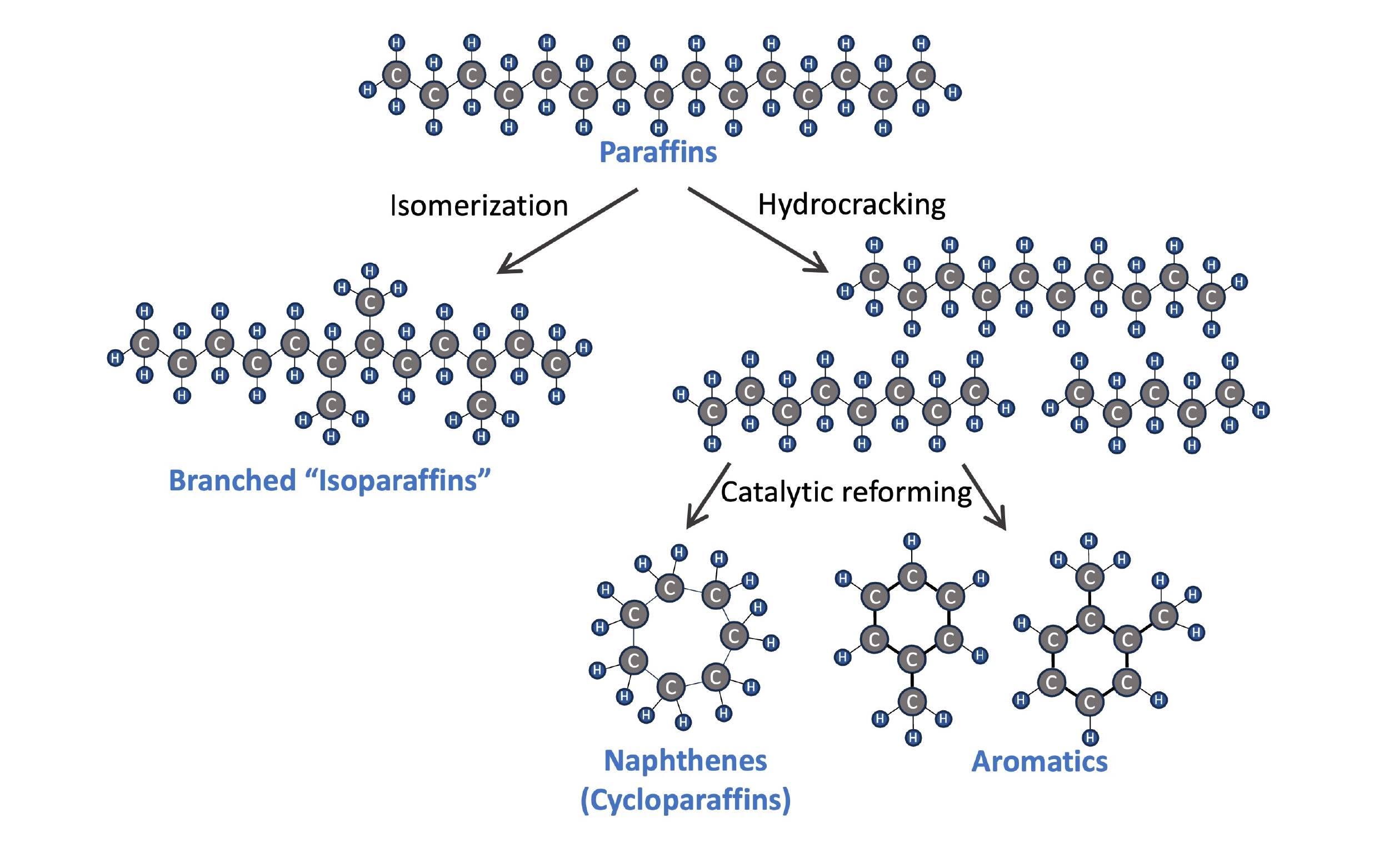
Four types of hydrocarbons (paraffins, isoparaffins, naphthenes, and aromatics) and three oil refinery operations that alter the hydrocarbon composition in fuel.
ASTM International is the entity that sets standards and performance criteria for aviation fuel composition. One specification, for example, is that the melting/freezing point of jet fuel must be no higher than -40°C. Isoparaffins in the blend help to meet this spec, as they have much lower freezing points than paraffins of the same weight. It is also necessary for aromatics to comprise between 8-25% of the jet fuel. Because of the different solvent properties of aromatics versus paraffins, fuel compositions outside this range might cause shrinking or swelling of O-rings fitted in the fuel lines, resulting in fuel leakage, which would be a major problem. Making a fully drop-in SAF is therefore more complicated than producing one type of hydrocarbon.
Approaches to Producing Aviation-Compliant SAF
There are a number of companies and approaches to produce SAF from different feedstocks, and recent articles review them in detail. But briefly, most approaches can be grouped into one of three categories based on the final step to transform chemical precursors to hydrocarbons:
- HEFA (Hydroprocessed esters and fatty acids): Conversion of vegetable or animal fats/oils, such as used cooking oil.
- AtJ (Alcohol-to-jet): Conversion of alcohols, such as ethanol or methanol, in a multistep process. The actual processes and catalysts differ depending on the alcohol (methanol, ethanol, isobutanol) but share broad similarities in the types of catalysts used. The alcohols may be from the fermentation of corn or other sugars or could be synthesized from CO2 and electricity using new electrolyzer technologies.
- FT (Fischer-Tropsch process): Conversion of synthesis gas, or “syngas”, a mixture containing both hydrogen and carbon monoxide in a ~2:1 ratio. The syngas could be produced from the gasification of biomass, or using green hydrogen and CO2.
These categories could be further split based on whether the precursors come from biomass feedstocks (biofuels) or synthesized from CO2 in a PtL process. Other methods that don’t fit in these three categories include pyrolysis of woody biomass or hydrothermal liquefaction of wet organic matter such as sewage or algae. Those methods result directly in a crude oil-like mixture which could be further refined.
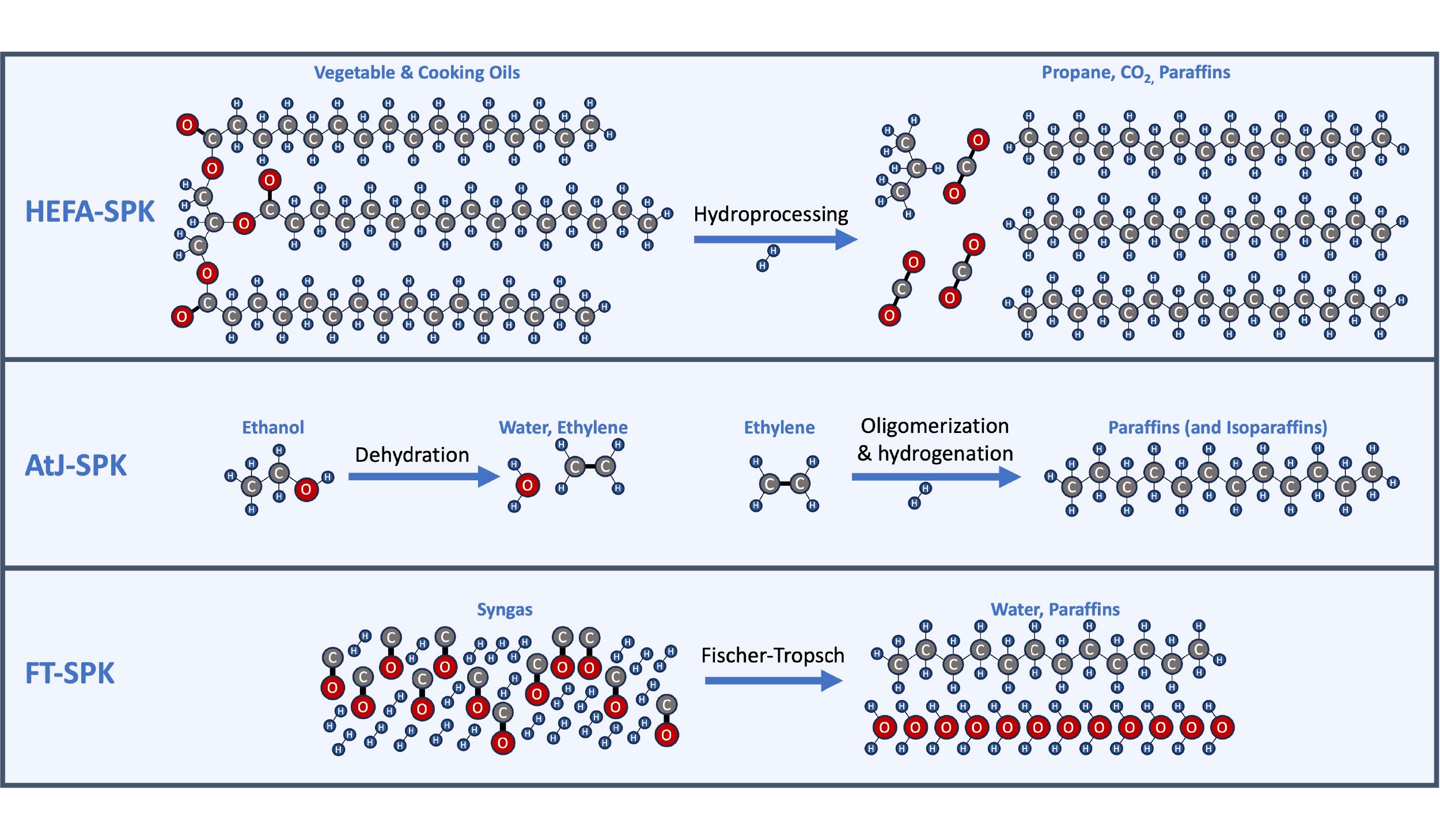
Three major routes and example schemes for producing synthetic paraffinic kerosene (SPK): Hydroprocessing of esters and fatty acids (HEFA), exemplified here by Honeywell/UOP’s Ecofining process; Alcohol-to-jet (AtJ), exemplified here by LanzaJet’s ethanol-to-jet process; Fischer-Tropsch (FT) catalytic synthesis of paraffins from syngas (a mixture of hydrogen and carbon monoxide).
Each SAF production approach uses special catalysts and reaction conditions to effect the respective transformation, and the output of each is primarily paraffins. Refinery operations like hydrocracking, isomerization, and distillation can be used to formulate a product in the kerosene (~8-16 carbon chain) range, but still with little or no aromatics. The resulting “synthetic paraffinic kerosene,” or SPK, is approved for up to 50% blending with fossil jet fuel. Standard fossil jet fuel is ~17% aromatics, so even a 50% blend of SPK retains the minimum 8% needed.
The low aromatic content of synthetic paraffinic kerosene actually makes it cleaner burning than its fossil counterpart in ways that impact both air quality and climate change beyond CO2 emissions.
Aromatics don’t always fully combust and may leave behind smog particulates. These can nucleate aviation contrails that function as a kind of thermal insulation in their own right. By some estimates, these aviation contrails may contribute to atmospheric warming to the same extent as the CO2 emissions themselves. So more substitution of fossil jet fuel with SPK brings immediate climate and environmental benefits.
In the long term, achieving 100% SAF will require new methods of producing or upgrading SAF to contain aromatics, or else upgrading all fuel line O-rings to a new material so that aromatics are not required. The company Virent already has a process to synthesize aromatics from plant-based sugars, approved as synthetic aromatic kerosene (SAK). Virent supplied SAK for Virgin Atlantic’s recent 100% SAF-based flight from London to New York, conferring 12% aromatics alongside the 88% HEFA supplied by AirBP. The groundbreaking flight offered a demonstration of the aspirational future of air travel.
The Road to Affordable SAF: A Feedstock Cost Analysis
At a price of only ~$2.50-$3.00 per gallon, jet fuel is cheap. Yet airlines often still have very thin margins, and despite aggressive targets for adopting SAF it won’t be realistic for airlines to pay any significant premium on fuel.[1] Are any routes to SAF cost-competitive with fossil jet fuel, and if not, could they ever be?
The cost of producing SAF with any given method depends on many factors, and assessing the contributions of capital, utilities, feedstock, and other fixed and variable costs to SAF price would entail a full technoeconomic analysis. But a simple treatment based on feedstock costs alone can give great insight into which approaches to SAF might be most promising. This section compares the costs and other challenges of using different feedstocks for SAF (e.g. oils, alcohols, syngas), beginning with biomass before turning to e-fuels, or SAF made from CO2 and electricity.
Vegetable or Cooking Oils (HEFA)
The HEFA pathway can be used to produce SAF from vegetable oils like soybean or corn oil, used directly or collected after use as cooking oil. This is the primary production pathway for SAF now, and is expected to fulfill the majority of expanded capacity through the decade to meet 2030 targets of ~5% of total jet fuel consumption (~5 billion gallons or 14 million tonnes). Beyond that, however, the supply of these oils will be constrained (there is only so much cooking going on at your favorite fast food restaurant), and it is already becoming so.
Used cooking oil for biofuel has been as low as $550/t in 2019, but has more recently risen to the $1100–1700/t range. Due to the inherent chemistry of, for example, Honeywell-UOP’s Ecofining process, the maximum possible yield is ~0.8 tonnes of paraffin per tonne of feedstock oil. Assuming $1100/t feedstock oil, a lower bound for HEFA price would be ~$1400/t or $4.15/gal. To reiterate, this lower bound reflects only the contribution of the oil feedstock toward final cost. SAF currently retails at nearly $7/gal, so there seems to be room for costs to come down, but there does not seem to be a path for HEFA to reach cost parity with fossil jet fuel in the absence of subsidies or drastic changes in feedstock price.
Ethanol and Sugars (Alcohol-to-Jet)
LanzaJet developed a process to convert ethanol into SAF by first dehydrating with a catalyst to produce ethylene gas. Ethylene is oligomerized with another catalyst to produce heavier olefins, which are hydrotreated to yield paraffins and isoparaffins. The process was developed to utilize ethanol produced from parent company LanzaTech’s microbial gas fermentation, in which carbon monoxide-rich industrial waste gases are used as an energy and food source by special microbes, but it is also applicable to ethanol from standard corn and sugarcane fermentation. Similar chemistry is employed by Vertimass and Gevo to produce SAF, respectively, from ethanol and isobutanol.
The current market price of ethanol is ~$1.70/gal, which is the lowest in 3 years but closer to historical values. A maximum yield of ~0.6 gallons SAF per gallon ethanol is possible based on the chemistry, which suggests a SAF cost lower bound of $2.83/gal. This is lower than HEFA and would seem to be near cost parity with fossil jet fuel, but this neglects any capital or operating costs. Whereas HEFA production is operationally simple, the AtJ process is multistep. Whether US corn ethanol is even sustainable has also frequently been a contentious question. In fact, the Biden Administration’s recent decision to recognize an alternative methodology for calculating lifecycle CO2 emissions may be the only reason AtJ-SPK from corn-ethanol qualifies as SAF and is eligible for IRA credits. Ethanol from sugarcane may be a cheaper and more sustainable route.
Ethanol fermentation is a very efficient bio-industrial process. The yield is 1 gal ethanol from roughly 6 kg sugar, so a perfect AtJ process beginning from fermentable sugars would require ~10 kg to produce 1 gal SAF. Is it possible to bypass ethanol by genetically engineering microbes that eat sugars but convert them directly into jet-fuel range hydrocarbons rather than ethanol? This was precisely the vision of Amyris, which had aspired to ferment sugar cane directly into jet fuel using its engineered yeast but pivoted from that goal in the mid-2010’s and announced a restructuring in 2023. Even if some other startup could overcome the challenges and realize that vision, the maximum yield of any such fermentation cannot exceed ~1 gal SAF from 10 kg fermentable sugar, i.e. no higher than an AtJ approach.[2] Thus any fermentation-based approach is similarly constrained by the price of fermentable feedstock. The question, then, is whether an engineered microbe could more realistically achieve the maximum yields using lower operational and capital costs than the AtJ catalytic process.
On the other hand, companies like Air Company and Liquid Wind are innovating power-to-liquid processes that synthesize AtJ precursors like methanol or ethanol from hydrogen and CO2. Because the economics would be driven by the price of electricity and/or green hydrogen, that discussion is grouped below along with other PtL approaches.
Waste Biomass (Fischer-Tropsch and Others)
Compared with conventional vegetable oil and sugar/ethanol feedstocks, waste biomass like forest residues are much cheaper, as low as $60/ton, and aren’t at risk for a shortage. One approach to using it is gasification and Fischer-Tropsch, as employed by companies like Velocys. The feedstock is gasified by heating to a high temperature, with a low and controlled amount of oxygen and moisture. This produces a gas rich in CO and hydrogen, called synthesis gas (syngas). The H2 content in this gas is typically low, but can be adjusted through the water gas shift (WGS) reaction, where CO and steam react to synthesize H2, though at the expense of losing carbon as CO2. In this way, the syngas can be adjusted to the ideal composition for synthesis of paraffins in the Fischer-Tropsch reactor (H2:CO ratio slightly above 2).
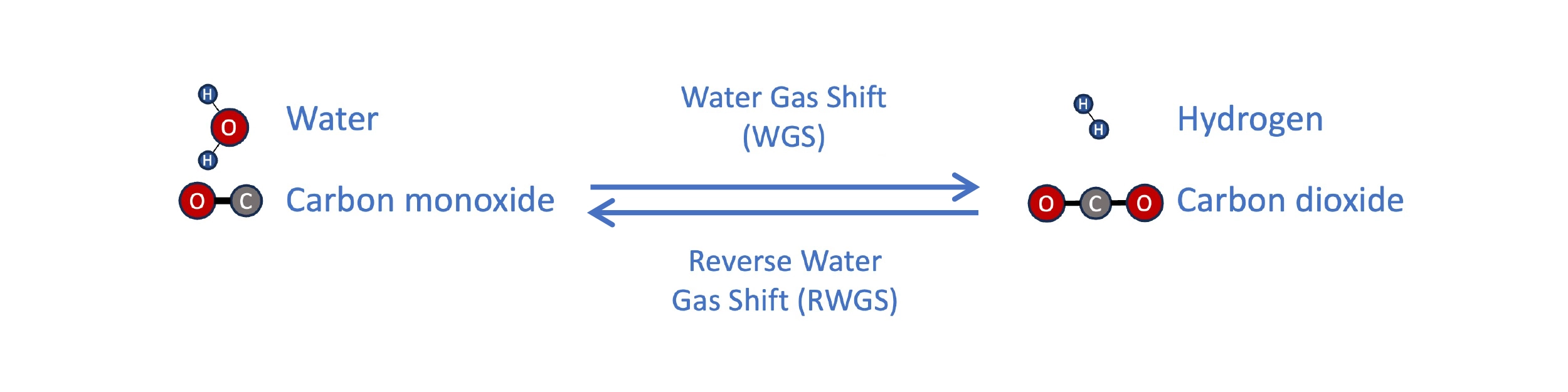
The water gas shift (WGS) reaction enables an increase in the H2:CO ratio of syngas. In a power-to-liquid process, the reverse water gas shift (RWGS) can be used to make syngas from CO2 and hydrogen.
Waste biomass feedstock is cheaper but has lower yields. Only ~0.15–0.2 tons of FT-SPK per ton of feedstock is achievable, so a forest residue price of $60/ton figures to a lower bound for SAF cost at ~$1.20/gal. This seems promising, so why haven’t Fischer-Tropsch fuels from waste biomass caught on? One challenge is the high capital costs of the gasifier and Fischer-Tropsch reactor. Both steps benefit from economies of scale, but sourcing enough consistent high-quality feedstock is a challenge. Solid feedstock is not as easy to transport as liquids like cooking oil or ethanol. The $60/ton price tag isn’t necessarily reflective of those collection costs. Plus, waste biomass is hardly pristine. It must be thoroughly dried, and dirt and leaves may cause problems in the gasifier. The raw syngas may require multi-step cleanup to remove contaminants before it is ready for use.
Other technologies like Alder Renewable’s fast pyrolysis might better fit the challenges of these feedstocks. Another possibility for a step function change in economics would be improved technologies to break down the recalcitrant cellulose of woody or grassy biomass into fermentable sugars. This has been a long-standing dream, but the high price of cellulase enzymes coupled with the quantities required has made it impractical. Companies like Blue Biofuels and others hope to finally crack the code with new technology, and if they succeed it could have a major impact, lowering the cost of the fermentable sugars themselves, and thus the price of ethanol, AtJ-SPK, and any other fermentation-derived product that could be envisioned. Whatever the approach, the IEA estimates enough sustainable biomass supplies to support ~380 billion gallons of liquid fuel production if we can only find a way to make the economics work.
Electricity & CO2 (Fischer-Tropsch, Alcohol-to-Jet)
The biofuel routes to SAF come with challenges and tradeoffs between feedstock prices and operational complexity and costs. What about power-to-liquid approaches that promise to produce SAF from just (low-carbon) electricity and CO2? There are different paths to go about it, but they all end up at nearly the same fundamental calculus of inputs: In the ideal case, about 9.5kg CO2 and 56–67 kWh of electricity are needed to produce 1 gallon of e-fuel.
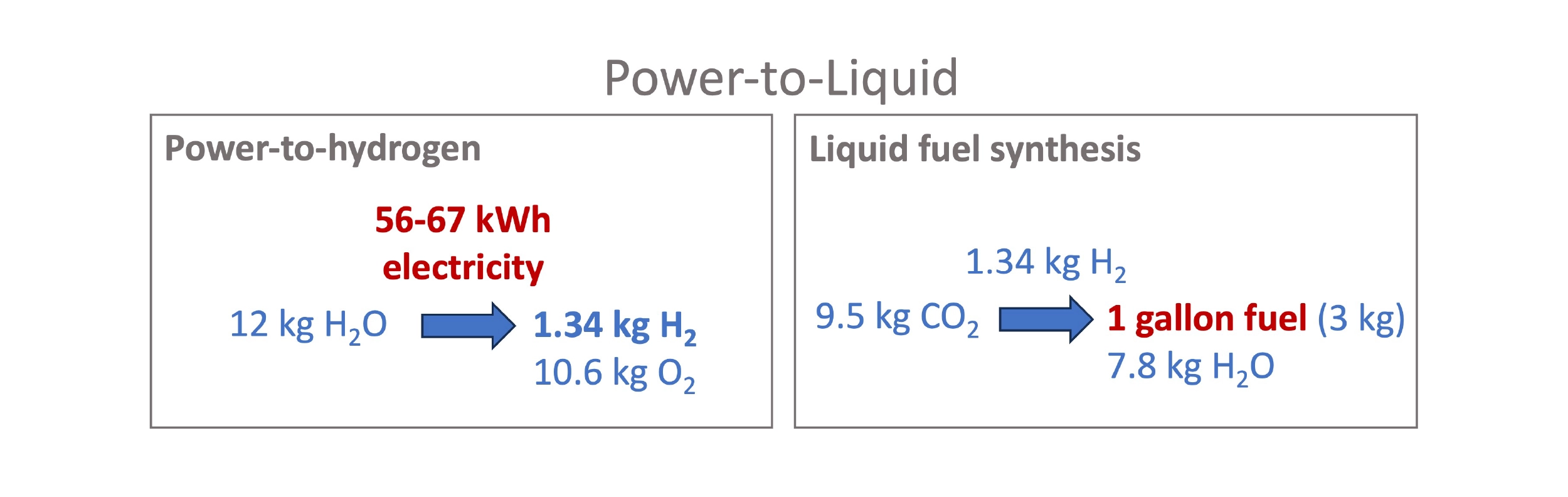
Generalized power-to-liquid (PtL) scheme, normalized to 1 gallon fuel.
For example, the most standard PtL method is to produce H2 using electrolysis of water and react with CO2 to form syngas by the Reverse Water Gas Shift (RWGS). At very high temperatures, the WGS reaction can flow in reverse, favoring the formation of CO from H2 and CO2. The resulting syngas can then be used for Fischer-Tropsch synthesis. The energy efficiency of H2 production is currently ~50 kWh per kg of H2 produced, though emerging tech, like that of startup Hysata and many others, might realize ~15-20% higher efficiencies. This means ~56-67 kWh of electricity are needed to produce 1.34 kg H2, which is the amount that must be combined with 9.5 kg CO2 to make 1 gallon of liquid fuel.[3]
There are other methods, like catalysts to synthesize alcohol from H2 and CO2 or novel CO2 electrolyzers to make CO directly, which are highlighted in the next section. But the amount of electricity and CO2 needed for any PtL approach is roughly the same regardless, assuming the method is operating with perfect efficiency.
How does this translate to cost? The cost of capturing CO2 depends on source and purity, ranging from $20/t for the CO2 emitted from ethanol plants (among the purest) to likely >$200/t for “direct air capture”, where CO2 is pulled directly from the atmosphere. A reasonable benchmark for discussion is $70/t, as this is around the cost of capturing emissions from cement, steel, and power plants, and also reflects the aspirations of emerging companies aiming to bring direct air capture below the $100/t mark. With that benchmark, captured CO2 contributes ~$0.67 toward one gallon of e-fuel, and the rest of the cost depends on clean energy pricing. (In reality, the captured CO2 cost is also coupled to energy prices, as an additional ~11 kWh per gallon fuel may be associated with capturing the CO2 used.)
Comparing the cost curve of PtL from CO2 to the lower bound prices for HEFA and ethanol AtJ, clean electricity would need to be priced at ~5 cents or 3 cents per kWh, respectively, for e-fuel to compete with these biofuel routes. Utility prices from the grid are certainly not that cheap, but renewables during peak hours of production may be on par.
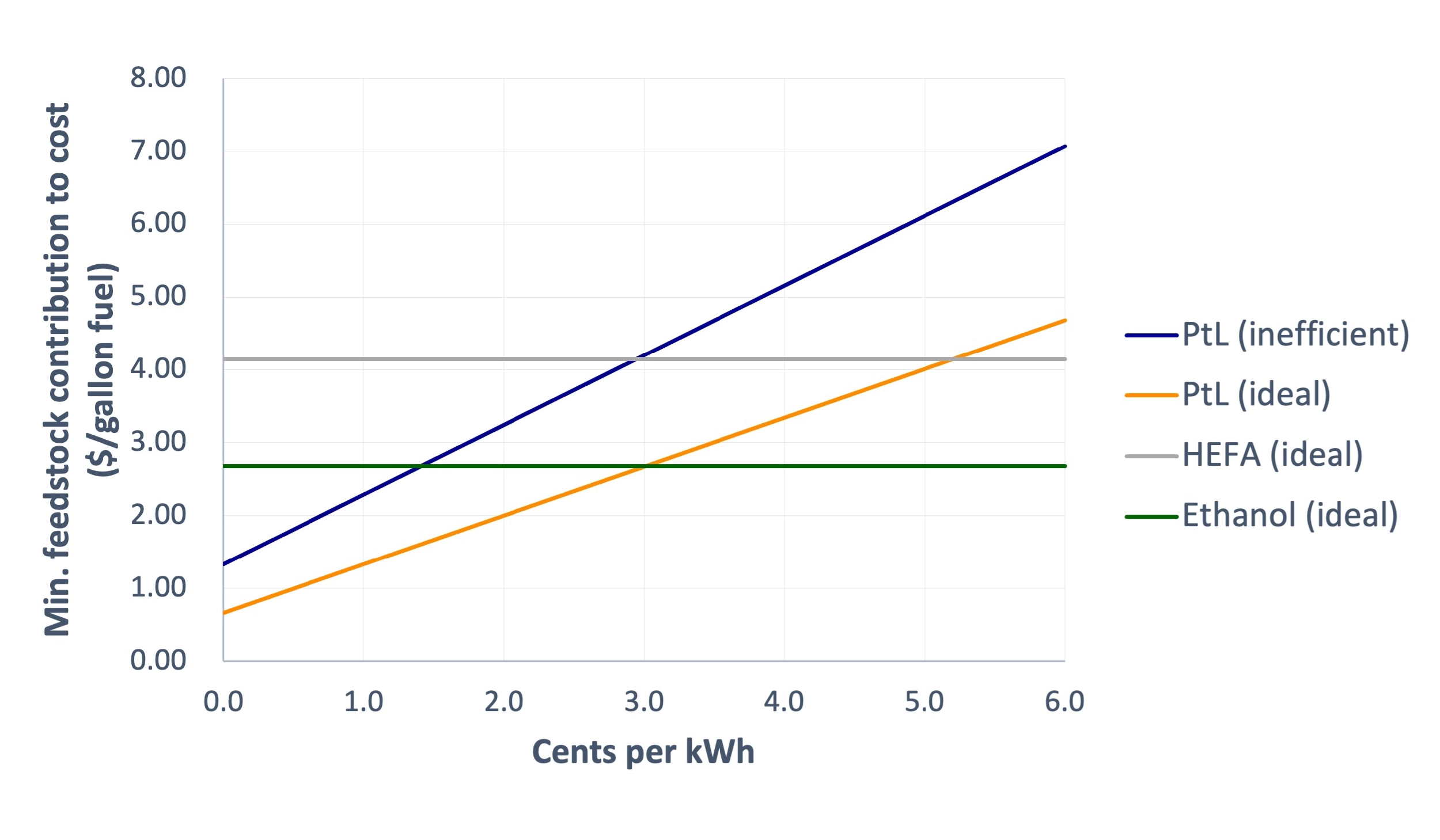
Comparison of feedstock contributions to cost of 1 gallon of fuel made from HEFA, ethanol (AtJ), or power-to-liquid (PtL). HEFA and ethanol use the assumptions described previously. The PtL curves assume captured CO2 at a price of $70/t. PtL is modeled as both ideal (1.34 kg H2 and 9.5 kg CO2 needed) or inefficient (1.91 kg H2 and 19 kg CO2 needed), and both assume electrolysis efficiencies of 50 kWh/kg H2.
This all assumes an “ideal” case, where the process proceeds with its maximum possible yield. How feasible is that? One technoeconomic analysis from Argonne National Laboratory modeled liquid fuel production from H2 and CO2 and Fischer-Tropsch. In the model, ~50% of the CO2 and ~30% of the H2 used in the process did not end up in liquid fuel at the end. There were a number of modeled inefficiencies, but three that stood out were:
- Low extent of conversion in the RWGS reaction, necessitating CO2 recycling (to enable multiple passes through the reactor)
- Only ~80% efficiency of the CO2 recycler/separator, so some CO2 is lost
- Only ~75% conversion of CO in the Fischer-Tropsch reactor to liquid fuels (and no way to recycle CO)
Comparing the “inefficient” and “ideal” PtL cost curves in the plot above shows how this “inefficient” (but maybe more realistic) process would impact cost. In the non-ideal PtL process, clean electricity must now be available at only ~1.5–3 cents per kWh to compete with biofuel routes, a much tougher challenge.
Summary of Cost Analysis: Efficiency is Everything
Fossil based jet fuel is cheap, but amongst the dizzying array of SAF production methods and feedstocks, there seem to be paths to get close to cost parity. Still, this first-order analysis made sweeping generalizations, ignoring capital costs and assuming scenarios where processes run with perfect efficiency. It was also unrealistic in assuming that liquids output from these processes are all useable as SAF. In reality, the Fischer-Tropsch reaction and similar processes will output a range of paraffins in the naphtha, kerosene, and diesel ranges, not to mention solid waxes that need to be treated by hydrocracking to make useable liquid fuel. Perhaps only half of the liquid fuel produced will be kerosene jet fuel. To be in the business of SAF will therefore entail being in the business of sustainable naphtha and diesel as well, though these might not have equivalent value in the market.
A top-down energy perspective further illustrates how critical it will be to innovate high-efficiency solutions.
If nearly 70 kWh of electricity is needed to produce 1-gallon SAF, it will take ~1700 TWh of clean electricity to produce the ~24 billion gallons of jet fuel we now consume annually in the US.
This is about equal to the total electricity from renewables and nuclear we produce now. And that’s for a perfect process.
Emerging Technologies and Trends
Fortunately, the SAF innovation space is bustling with brilliant researchers and startups who are looking to address the challenges of sustainable transportation. Startups are developing enabling technologies such as novel reactors or CO2 electrolyzers, which can streamline SAF production processes and make them much more efficient. Some areas have stood out as particularly impactful for innovation: producing syngas, producing methanol, and other direct or streamlined approaches.
Improving Syngas Production for PtL
Syngas is the mixture of hydrogen (H2) and carbon monoxide (CO) used to produce liquid fuel in a Fischer-Tropsch reactor. In a power-to-liquid (PtL) process, the hydrogen can be produced by the electrolysis of water. The bigger challenge is synthesizing CO, which is not easy to do efficiently. The standard approach is the reverse water gas shift (RWGS), in which H2 and CO2 react to produce CO and water. This is a temperature-dependent, reversible reaction, and high temperatures are needed to convert more CO2 into CO. Even at 600°C, it is common for less than half of the CO2 to be converted to CO in a RWGS reactor. This is a major source of inefficiency in a PtL process.
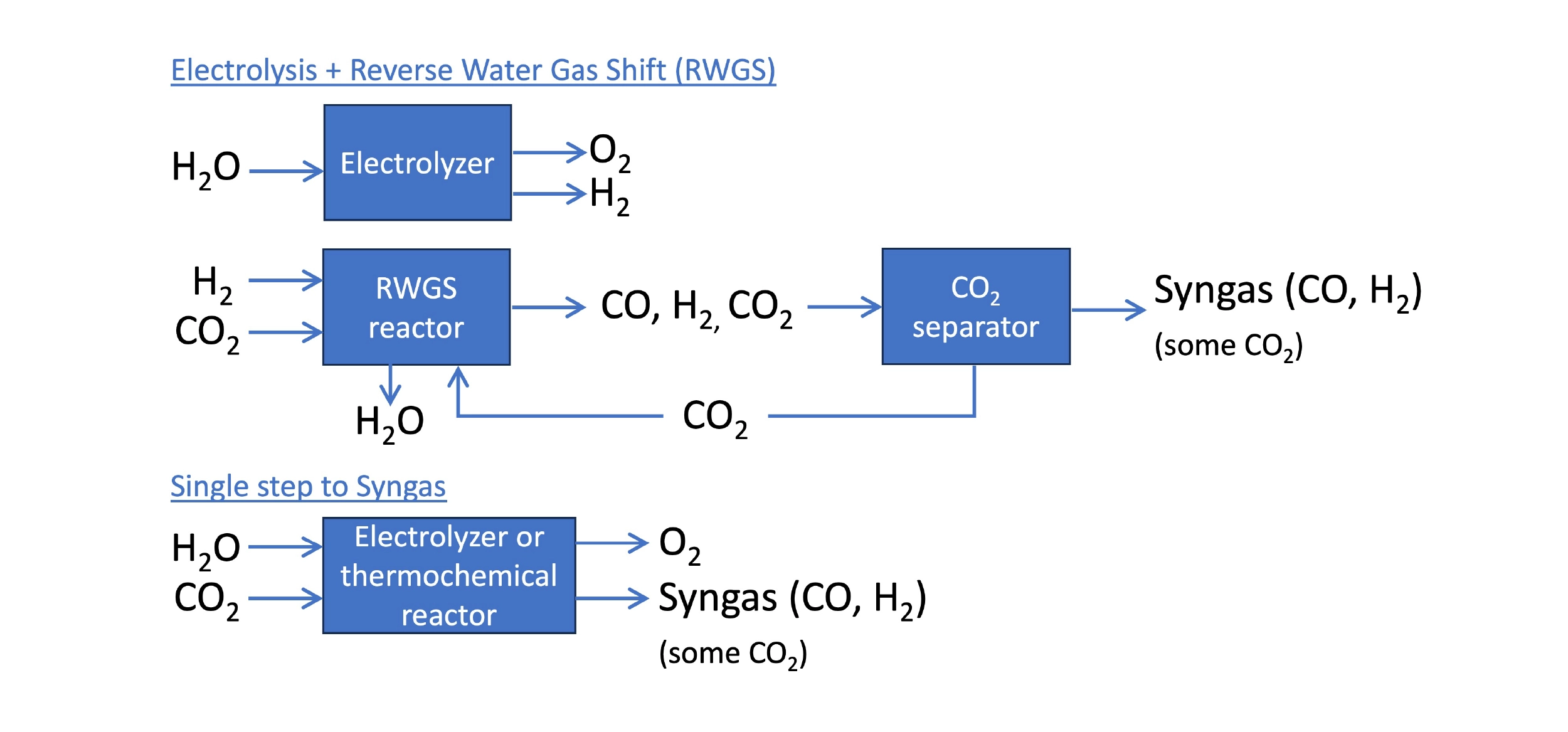
Approaches to synthesizing syngas using energy and CO2. The standard approach is electrolysis of water and the reverse water gas shift (RWGS) reaction. CO2 electrolyzers or new thermochemical reactors can produce syngas in a single step.
Improved RWGS
Lydian Labs is developing a more efficient RWGS reactor, which is resistively heated based on a novel catalyst material. This enables rapid and highly uniform heating to temperatures of ~1000°C in a matter of minutes. Lydian Labs believes they can achieve among the most efficient total energy consumption for the CO production step (~2 kWh per kg of CO2 reduced), and with a level of conversion that would allow direct pass into a Fischer-Tropsch reactor (less than ~20% unreacted CO2). And even as competing technologies like CO2 electrolyzers become more efficient, they expect the low CapEx cost of their catalyst to be a sustained advantage.
CO2 Electrolysis
Direct electrolysis of CO2 is an alternative to RWGS that can consolidate syngas production to a single step, reducing capital and operational costs. Although an emerging tech, CO2 electrolyzers employ the same technologies seen in green hydrogen tech – aqueous alkaline, polymer membrane, or solid-oxide electrolyzer cells (SOEC) – and can usually function to co-produce hydrogen as well.
Of the types of electrolyzers, SOECs are understood to have the potential for the highest energy efficiency. The drawbacks to SOECs are the capital costs and the need to operate at high temperatures, given that the ceramic electrodes do not hold up well to frequent cooling and re-heating. As a result, SOECs may be disadvantaged to use with intermittent energy sources, such as many renewables.
SeeO2 is one startup developing an SOEC that can produce CO and/or syngas. In the absence of water, they can convert CO2 to CO with high efficiency that could beat even the best H2 electrolysis followed by RWGS. And using CO2 and water as co-inputs, they can produce syngas directly, with control over the H2:CO ratio. Beyond SAF, it’s worth noting that carbon monoxide has its own established markets in the polymer (polyurethane) and steel manufacturing industries as well. Some efforts to decarbonize steel production have focused on new systems which use H2 rather than coke (i.e. coal), but SeeO2’s technology could use CO as a near drop-in with current infrastructure, and with as good or even better efficiency than H2.
Thermochemical Approaches
OMC is taking a different approach to produce H2 and syngas. OMC’s thermochemical reactor can convert water to H2 or convert water & CO2 to syngas using heat energy rather than electricity. The heat could be generated from electrical heating, but it could also come from sources like solar heating or waste heat from industrial processes such as steel manufacturing. This creates the possibility for total energy efficiencies exceeding what could be achieved by electrolysis.
OMC’s reactor also uses simple, cheap materials (metal oxides) and is easier to scale to large volumes compared to electrolysis cells. This latter point is potentially a major advantage of a thermochemical approach like OMC’s. Because electrolysis relies on the surfaces of electrodes, scaling to larger production capacities entails stacking many electrolysis modules, which means a linear correlation between capital costs and scale. This doesn’t leverage the economies of scale that are possible for a fluidized bed reactor like that used by OMC.
Other approaches to produce syngas without using electricity take advantage of sustainable biogas (methane) from manure or from composting facilities. Synhelion and Caphenia are two companies innovating high-temperature reactors that can convert a mixture of methane (CH4) and CO2 into syngas (CO and H2). This allows CO2 to be captured while also leveraging methane that would otherwise escape and amplify climate warming.
Methanol As a Precursor and As a Fuel
Much of the technology to produce SAF is part of an ecosystem of approaches enabling the synthesis of other renewable fuels and chemicals. One such product that is catching increasing attention is methanol. Methanol can be converted into SAF through a multi-step process which uses similar catalysts as other alcohol-to-jet processes. A related (in fact, older) process by ExxonMobil can convert methanol into gasoline as well, and the startup P1 Performance Fuels is commercializing an improved methanol-to-gasoline process that outputs truly drop-in gasoline. Dimethyl ether, a gaseous intermediate in the methanol-to-jet conversion, could itself serve as a replacement for residential propane. Oberon Fuels is commercializing its production from renewable biogas. Finally, methanol is of interest as a liquid fuel in its own right, especially for the shipping industry.
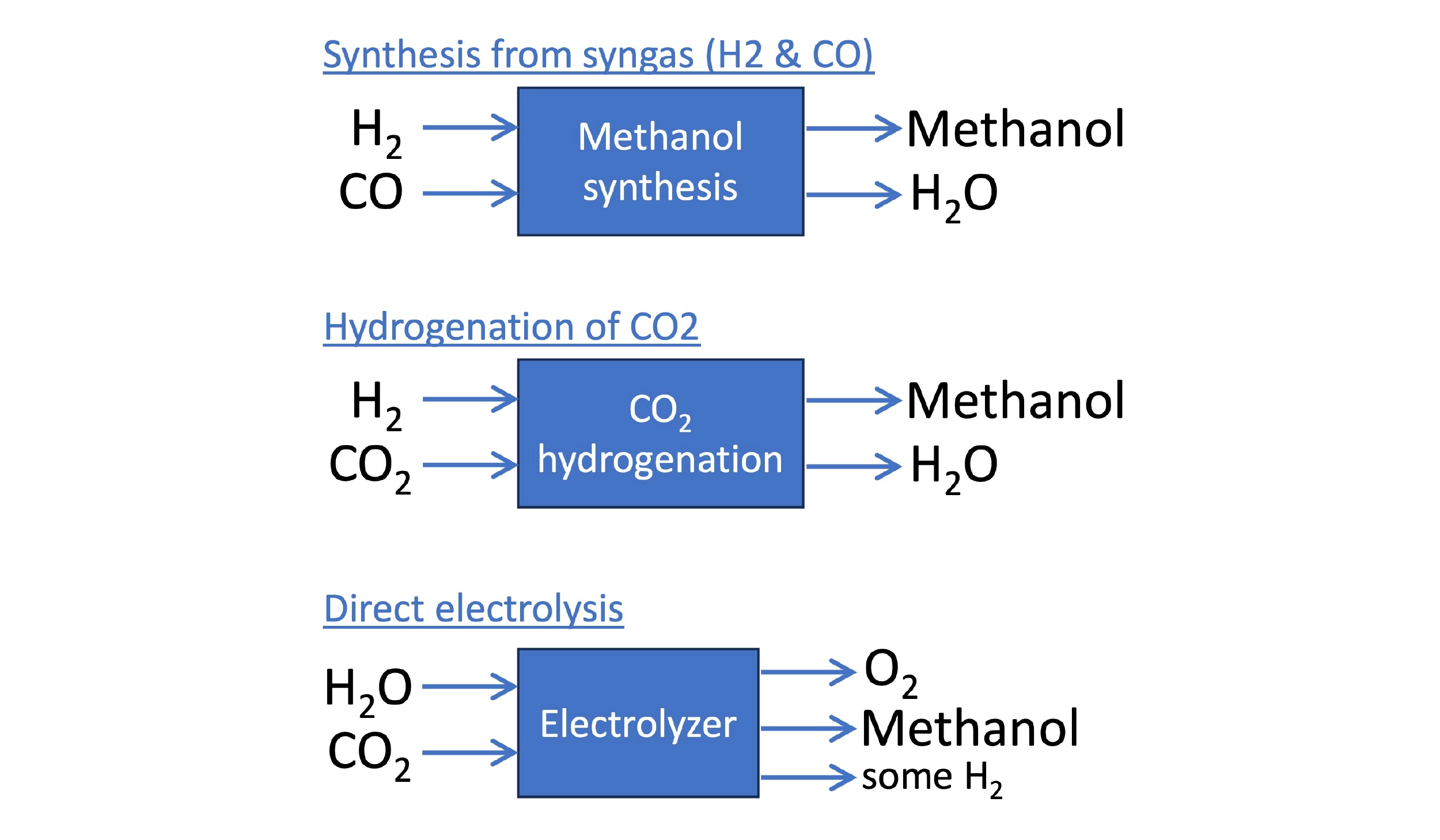
Approaches to synthesizing methanol. Methanol can be synthesized from syngas, but newer tech allows the direct hydrogenation of CO2. Direct electrolysis enables the production of methanol from water, CO2, and electricity in a single step.
Just as diverse as the uses for methanol are the technologies emerging to produce it. Methanol can be synthesized from syngas (similar to, but using a different catalyst than Fischer-Tropsch), but newer approaches allow the synthesis of methanol directly from H2 and CO2, with greater efficiency. Germany-based ICODOS is taking this a step further by integrating aspects of the methanol production process with the CO2 separation and capture from waste gases. The methanol/water output also functions as a solvent for CO2 absorption, for example, while the input H2 stream facilitates CO2 desorption. The integration allows nearly 100% utilization of the CO2. Oxylus Energy has developed an electrolysis catalyst that can produce methanol directly from CO2 and water, removing the need for an additional H2 or syngas production step.
Unlike Ethanol-to-jet, the Methanol-to-jet process is actually not yet an ASTM-approved pathway to produce SAF, though it is likely only a matter of time. But there is benefit in having multiple fuel molecules (methanol, dimethyl ether, gasoline, SAF), with their distinct advantages and use cases, all closely linked in a value chain. And innovations that make methanol synthesis cheaper and more efficient are transformative for the industry as a whole.
Consolidated Approaches to e-Fuel
OxCCU has developed a Fischer-Tropsch-like catalyst that can produce SAF directly from H2 and CO2. This approach bypasses the need for intermediates like syngas, CO, or methanol entirely, although the H2 would still need to be generated by electrolysis of water. OxCCU’s catalyst is also based on iron, a cheaper and more sustainable metal than the cobalt more commonly used in Fischer-Tropsch reactors.
Prometheus is building an integrated fuel synthesis platform using direct CO2 electrolysis and alcohol-to-fuel technology. The system employs technology from Oak Ridge National Laboratory to capture CO2 and convert it directly into long-chain alcohols – e.g., butanol or hexanol. The long-chain alcohols are separated from water using an innovative and efficient separation membrane made from carbon nanotubes, and then converted with a catalyst to hydrocarbon fuel (primarily gasoline as opposed to SAF). The company’s bold claims have raised skepticism, as they’ve announced plans to produce hundreds of thousands of modular units by the end of the decade which could collectively produce ~50 billion gallons of fuel.
Considerations for Investors
As we’ve spoken with startups and experts, we’ve compiled some questions to evaluate innovations in the SAF space. In addition to the operational advantages or constraints of the tech, it’s important to understand the potential ease or difficulty of deploying the tech at scale. And of course the maturity of the tech should match the stage of investment and level of risk of interest to the investor.
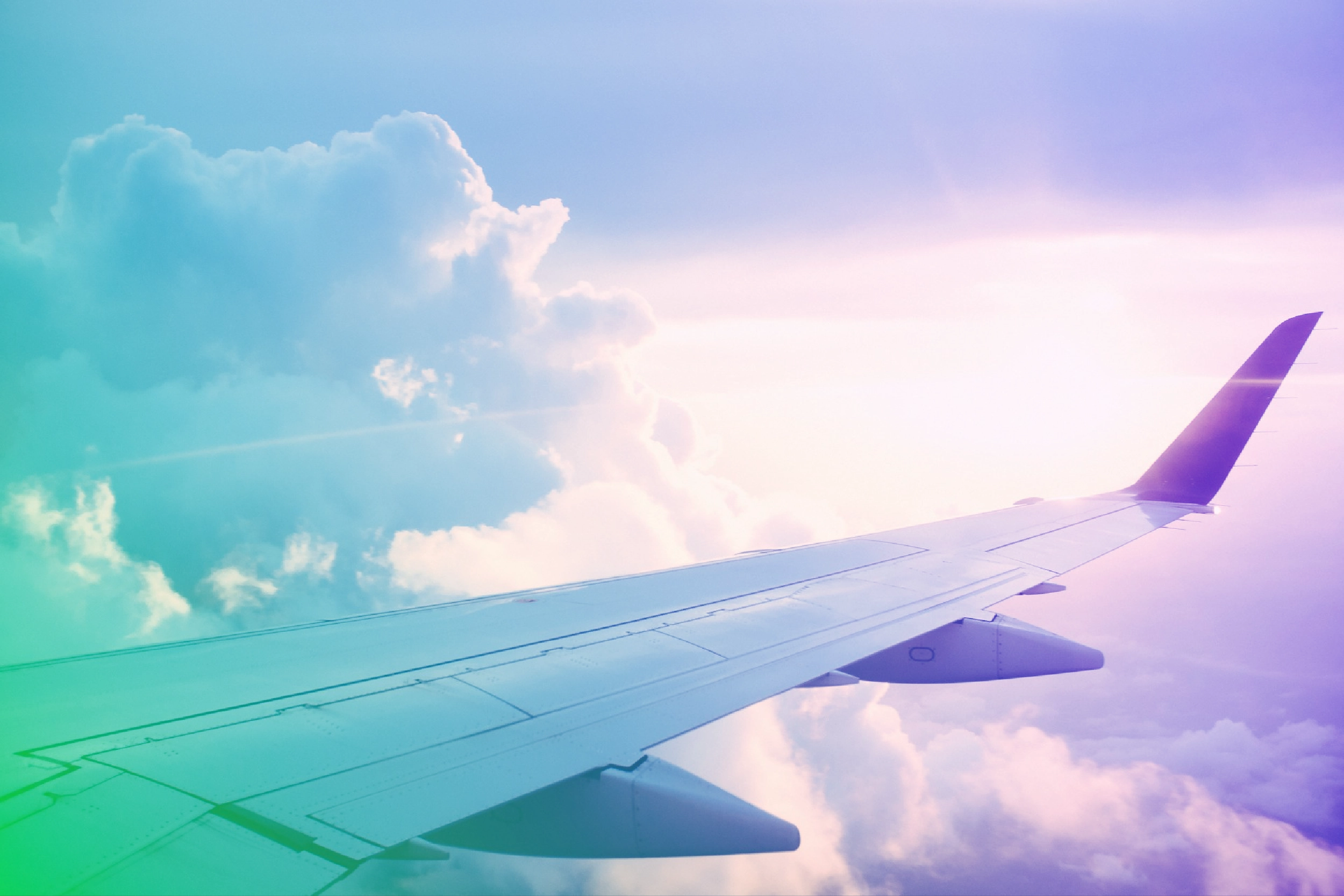
Operational Tech Advantage
- How do your tech advantages translate to value? What price point for SAF is attainable with this innovation? How does that compare with other SAF and market prices for regular fuel?
- What is the efficiency of your catalyst or system (e.g. mass of product versus quantity of energy or feedstock input)? How does this compare with competitors?
- What is your feedstock? Is the supply scalable? How sensitive is the catalyst or system to varying feedstock spec?
- What are your assumptions for electricity price and intermittency/availability?
- What comes out the other end of the reactor? Is it a mixture of compounds? Is further purification required?
- For systems that integrate carbon capture with conversion to a product: Why is this advantaged? Are you just co-locating two operations, or is there real synergy in the chemistry/physics enabled by this integration?
Deployment Advantage
- Does your catalyst or system use expensive/rare metals or other expensive materials?
- Is it a standard form factor that is easy to manufacture? How large of a system is required for the economics to work?
- How significant will manufacturing/capital cost be? How does it change with increasing production scales (e.g., 1 million gallons, 50 million gallons)?
- What partnerships will be required to go to market and what is the status of those relationships?
Maturity of the Tech
- How much product (methanol, syngas, fuel, etc.) have you produced?
- How long have you run the catalyst or system and in what conditions?
- What are the risks/uncertainties at the next levels of scale? Is there still scientific risk or just engineering risk?
Conclusion: SAF Innovation Can Make a Difference
Sustainable aviation fuel is becoming a reality, with the help of government incentives like the Inflation Reduction Act and using technologies that already exist. Large scale adoption of SAF, however, will require two things: abundant, cheap clean energy and highly efficient processes and catalysts to synthesize fuel.
The constraints of energy supply must be addressed by other industries, but there are innovations – more efficient and selective chemistries and more integrated processes – that can move the tipping point to large scale SAF production.
Identifying and investing in the best ones and stacking them together could make a real difference in accelerating a transition away from fossil fuels and creating a cleaner world.
Landscape
Biofuels – HEFA
Honeywell/UOPWorld Energy
Braya Renewable Fuels
Aemetis
SkyNRG
Neste
BP Repsol
Biofuels – Alcohol-to-Jet
GevoLanzaJet
Vertimass
Biofuels – Fischer-Tropsch
Fulcrum BioenergyEnerkem
Velocys
Neste
Biofuels – Other
ViridosVirent
CleanJoule
Alder Renewables
Firefly
e-Fuel – Methanol-to-Jet (or Gasoline)
MetafuelsTopsoe
HIF Global
P1 Fuels
e-Fuel – Fischer-Tropsch
Dimensional EnergyInfinium
Spark e-Fuels
INERATEC
Syngas Synthesis – Reverse Water Gas Shift
Lydian LabsTopsoe
Syngas Synthesis – CO2 Electrolyzer
SeeO2Twelve
Sunfire
Syngas Synthesis – Thermochemical
OMCSusteon
Caphenia
Synhelion
Methanol/Alcohol Synthesis – From H2/CO2
ICODOSAir Company
Refuel.green
Liquid Wind
Methanol/Alcohol Synthesis – CO2 Electrolyzer
OxylusPrometheus
Other Consolidated Approaches
OxCCUNotes
[1] Compare ~$20 billion in global airline profits in 2023 to ~100 billion gallons jet fuel consumed. A change of 20 cents per gallon fuel would wipe out profits if costs were not passed on to consumers.
[2] Based on a balanced chemical equation using dodecane (C12H26) as a stand-in for SAF:
37 Glucose (C6H12O6) → 12 C12H26 + 78 CO2 + 66 H2O
The maximum yield is ~3 kg SAF per 10 kg glucose, and ~3 kg SAF = 1 gal
[3] Based on a balanced chemical equation using dodecane (C12H26) as a stand-in for SAF:
12 CO2 + 37 H2 → C12H26 + 24 H2O